From aquaculture to sustainable fisheries, UNH researchers are involved in various multidisciplinary projects.
Current CSSS Projects
NOAA Fisheries provides engineering expertise to the U.S. aquaculture industry. Working with collaborators, we are filling gaps in engineering standards for offshore aquaculture structures and developing on-demand gear that is safer for protected species.

Overview
We are developing offshore aquaculture engineering guidance to support the domestic aquaculture industry and make the permitting process more efficient. We are also studying the feasibility of using on-demand gear for shellfish aquaculture.
Research Questions
Offshore Aquaculture Engineering Guidance
- What are the most critical gaps in engineering standards for offshore structures used in aquaculture?
- How can we fill the most critical gaps in offshore aquaculture engineering guidance? How can we use this guidance to increase efficiency in the permitting process?
- What are the needs of the aquaculture industry?
- What are the needs of our federal regulatory partners?
Developing On-Demand Aquaculture Gear
- Is it economically viable to aquaculture oysters, blue mussels, or sea scallops using on-demand gear (e.g. costs and expected revenue)?
- Is it economically and technically feasible to culture oysters, sea scallops, or mussels in deep water/exposed conditions, as measured by growth rates and survival?
- How do we optimize on-demand gear for aquaculture uses (e.g., improving gear design, maximizing stocking densities) and improve operational efforts?
- What are the hydrodynamic effects of storm events on offshore aquaculture gear?
Project Description
NOAA Fisheries aims to bolster sustainable aquaculture in the United States. Engineering can help accomplish this goal by developing science and systems that support the emerging offshore aquaculture industry.
Offshore Aquaculture Engineering Guidance
NOAA’s offshore aquaculture engineering working group developed methods for creating offshore aquaculture engineering guidance. The guidance will support the permitting process. This group took on the following tasks:
- Engaging with pertinent federal regulatory agencies including the Army Corps of Engineers
- Understanding the needs of aquaculture industry members and federal partners
- Identifying gaps in the peer-reviewed literature and engineering standards with respect to U.S. offshore aquaculture engineering
- Developing an approach to quantify the structural integrity of an offshore aquaculture farm by conducting a case study
This work supports Goals 1 and 2 of the NOAA Aquaculture Strategic Plan (2023–-2028):
- Goal 1: Manage Sustainability and Efficiency – Improve the regulatory process for sustainable coastal and marine aquaculture through collaboration with partners.
- Goal 2: Lead Science for Sustainability – Use world-class science expertise to meet management and industry needs for a thriving seafood production sector and share this knowledge broadly.
This project is funded by NOAA Office of Aquaculture and the Northeast Regional Aquaculture Center.
Developing On-Demand Aquaculture Gear
Marine aquaculture can increase domestic seafood production and support coastal economies. But some gear uses lines that could potentially pose a risk of entangling marine mammals and sea turtles. This currently limits where aquaculture can take place in the ocean. Although aquaculture does not have a history of entangling protected species in the United States, we are committed to proactively engineering gear that is safer for these protected animals. We are learning from challenges and innovation in the fixed-gear commercial fishing industry, such as “ropeless” or on-demand lobster gear currently in development. This gear reduces the number of lines in the water and the amount of time that the lines are present, reducing the risk of entanglement.
This project is funded by NOAA Office of Aquaculture and the Atlantic States Marine Fisheries Commission.
Study Methods
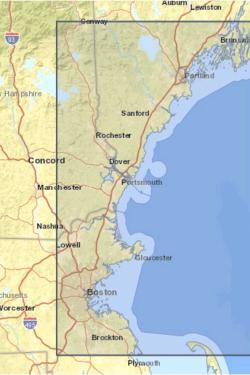
Offshore Aquaculture Engineering Guidance Case Study
We performed a case study showing how offshore aquaculture engineering guidelines can be applied to measure the structural integrity of a commercial mussel farm in the offshore waters of New England. We conducted the case study in two parts.
Part I: Quantifying Environmental and Extreme Weather Conditions for Use in the Engineering Design Process
We quantified the amount of energy that waves and currents can produce within the region of interest due to extreme weather events (for example, hurricanes, nor'easter storms, etc.). The goal was to understand the intensity of the extreme weather events in the area and the probability of them occurring so they could be applied in Part II. We did this by analyzing relevant historical storm intensity data (e.g. recorded wave heights and currents speeds) and developing probabilities of occurrences for a variety of wave and current intensities.
Part II: Using Validated Numerical Models to Estimate the Probability of Failure of a Continuous Longline Mussel Farm
We applied the information gathered in Part I to the engineering design process for the offshore mussel farm case study. First, we translated the wave heights and current speeds quantified in Part I to loads (i.e. forces) that can be analyzed in the design process. We then applied the design loads to the mussel farm within a validated numerical model simulation to assess the structural integrity. This process can identify the components of the mussel farm that are most likely to fail under extreme weather events. This knowledge is useful to the design engineer when attempting to achieve certain factors of safety within the design.
Similar to Part II of this case study for the mussel farm, our collaborators at the University of New Hampshire led a project to develop a numerical modelling technique for the engineering design analysis of a kelp (saccharina latissima) farm.
Field Tests for On-Demand Aquaculture Gear

We conducted field tests to assess the economic viability of using on-demand technology to culture bivalves in bottom cages in New England waters. We did this by integrating commercial off-the-shelf shellfish cages with on-demand technology. We tested a variety of on-demand systems with shellfish cages occupied by oysters, mussels, and scallops to determine the optimal combination of gear and bivalve species for the deep water/exposed conditions. During the field tests, we recorded bivalve growth rate and the following environmental conditions:
- Salinity
- Temperature
- Depth
- Dissolved Oxygen
- pH
- Chlorophyll
- Turbidity
- Waves
- Current speeds and directions
We developed a techno-economic model that considers cost, species cultured, survival and growth to help identify the conditions under which on-demand shellfish aquaculture is economically feasible.
Project Results

Offshore Aquaculture Engineering Guidance
Part I of this project provides a comprehensive analysis of extreme environmental conditions in New England's offshore waters. The results suggest a 10-year storm with a significant wave height of approximately 26 feet and a current speed of 5.5 feet per second, while a 50-year storm suggested a 30.8 feet significant wave height and 6.4 feet per second current.
Understanding the probability and intensity of extreme environmental conditions is a critical step when designing offshore aquaculture farms. The methodology we used is not unique to New England offshore waters; it can be used to understand extreme environmental conditions at almost any marine location. This phase is necessary to establish design parameters for the work conducted in Part II of this project, which will focus on applying the parameters to the engineering design process for an offshore mussel farm.
Developing On-Demand Aquaculture Gear
The results of the field tests suggested that scallops were the most economically viable bivalve for bottom cage culture in offshore environments using on-demand technology. The growth rates experienced for these conditions were at the higher end of expected growth rates for scallops. We also observed that shallow sites exposed to high energy from waves and currents are not viable for this farming method because of adverse impacts to the bivalves' health.
Our collaborators at the University of New Hampshire plan to investigate further by conducting additional field tests focused on improving the economic viability of this bivalve farming method (e.g. gear scalability and modifications, stocking density, etc.).
Contact Information
NOAA Project/Principal Investigator
Project Team
- David Fredriksson, University of New Hampshire
- Richards Sunny, A.I.S. Inc. in support of NOAA Fisheries
- Igor Tsukrov, University of New Hampshire
- Longhuan Zhu, University of New Hampshire
- Michael Chambers, University of New Hampshire
- Bill Silkes, American Mussel Harvesters
Collaborators/Partners
- University of New Hampshire
- New Hampshire Sea Grant
Project Advisors (Engineering Guidance)
- Toby Dewhurst, Kelson Marine
- Zach Mosicki, Kelson Marine
- Michael MacNicoll, Kelson Marine
- Corey Sullivan, Innovasea
- Mirjam Furth, Texas A&M University
- Cliff Goudey, CA Goudey & Associates
- Zachary Dovinski, Manna Fish Farms
- Javier Infante, Ocean Rainforest
Publications/Reports
Sunny, R.C., Fredriksson, D.W., Tsukrov, I., Zhu, L., Bowden, M., Chambers, M. and Silkes, B. 2024. Design considerations for a continuous mussel farm in New England Offshore waters. Part I: Development of environmental conditions for engineering design. Aquacultural Engineering (107) doi: 10.1016/j.aquaeng.2024.102476
The Center for Sustainable Seafood Systems is proud to continue the UNH Integrated Multi-Trophic Aquaculture program utilizing an innovative approach to responsibly raise seafood in NH. The Center recently transferred 2,000 rainbow trout from Ossipee, NH to New Castle, NH where they will grow as “steelhead” in an ocean pen along with sugar kelp and blue mussels.
As the fish grow, the kelp and mussels will extract nutrients produced by the fish. This method promotes a healthy coastal system as the Center conducts research and educates students and public alike about sustainable seafood. The fish will continue to grow throughout early 2024, until they are large enough to be brought to local markets.
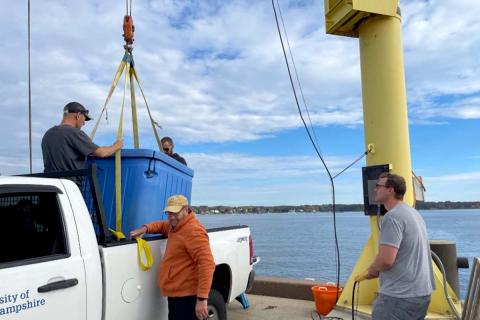



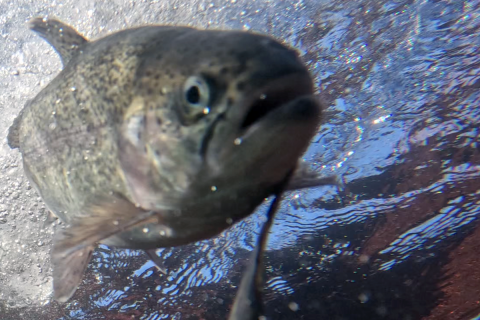
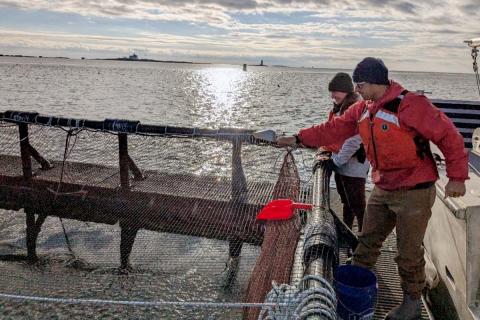
As described in the Center for Sustainable Seafood Systems mission statement, we strive to promote responsible seafood. As such, we adhere to strict guidelines and policies while working with vertebrate animals. Proper care, use, and humane treatment of animals is of the highest priority for our team. Not only are we guided by our mission, but we are authorized and held accountable by the UNH Institutional Animal Care & Use Committee (IACUC), an oversight committee that all vertebrate research at UNH must seek approval through.
AquaFort IACUC protocol number: 230804
For additional information on IACUC standards, guidelines, and approval process, please follow the link: IACUC.
For additional information on AquaFort and steelhead trout ethical treatment guidelines, please contact us.
With aquaculture as a rapidly growing source of food across the globe, UNH seeks to explore the cutting edge of aquaculture technology to ensure a responsible and sustainable future for the industry. Much like land-based agriculture, aquaculture can be done in ways that maximize the economic and health benefits to the community, while potentially benefiting the environment. One such technology is Integrated multi-trophic aquaculture, or IMTA. This method addresses concerns about nutrient loading in aquaculture by utilizing additional farmed products to remove excess nutrients, which typically enter the environment in the form of fish waste. In large fish farms, the waste from the fish add nutrients to the water, and in areas without much water flow, or areas that already have a high nutrient load, this could degrade water quality. With IMTA, additional products are grown with the fish, such as algae and shellfish, which will grow by removing and absorbing the excess nutrients. In NH, Dr. Michael Chambers with NH Sea Grant and the UNH School of Marine Science and Ocean Engineering have explored this practice in a model named AquaFort, which raises steelhead trout in net pens with sugar kelp and blue mussels on lines outside of the nets.

Species profiles
Steelhead trout (Oncorhynchus mykiss)
This salmonid species is native to the North American West Coast but has been stocked by state and federal hatcheries in rivers and streams for decades in the East for recreational anglers. Steelhead trout are diadromous fish, meaning they use both freshwater and saltwater habitats to complete their lifecycle. In freshwater, they are referred to as “rainbow” trout. When they get to salt water, they are then referred to as “steelhead”. The steelhead raised in AquaFort are hatched locally at the Sumner Summer Brook Trout Farm in Ossipee, NH, and transferred to a saltwater pen when they are close to 200 g. They can grow from 200 g to 4 kg in less than a year. These fish have a high market value, and show great potential to be an economically important fish in U.S aquaculture. These fish are sold to local seafood markets in Portsmouth such as Seaport Fish, Row 34 in Portsmouth and Sanders Fish Market.

Blue mussels (Mytilus edulis)
Blue mussels are a common bivalve species in North America. These shellfish can be farmed on various submerge or vertical ocean deployed systems. Since mussels are filter feeders, they take water in through their siphon, consume the organic material in the water, and pump out the clean water. This makes them a great co-species to raise with steelhead trout, as the mussels are able to consistently filter water through most conditions. When raising mussels in the North Atlantic, farmers must be aware of shellfish closures and restrictions, and be prepared for predation by birds, especially eider ducks. The mussels raised in AquaFort are wild mussels, meaning they are collected as wild larvae. This is done simply by deploying “fuzzy” rope, which provides extra surface area for larval mussels to easily settle on. After some time they grow on the line and begin filtering nutrients from the water.

Sugar kelp (Saccharina latissima)
Sugar kelp is a macroalgae species that is also common throughout the North Atlantic. This species is ecologically important because it provides habitat and nutrients for countless marine organisms. Farming of kelp has grown tremendously due to its nutritional benefits for people, has potential as feed for livestock and perhaps as a basis for producing biofuel. In AquaFort, this crop absorbs dissolved nutrients from steelhead trout. It also grows best throughout the Winter and Spring and therefore complements many fishing industries. Sugar kelp can come from recently selected strains, or wild strains that are grown on a seed line in a closed system. After it sets on the twine, it can be deployed in the farm. The sugar kelp found on AquaFort comes from Atlantic Sea Farms in Biddeford ME. When it’s ready to harvest, look for it at the Portsmouth Brewery, where it becomes an ingredient in their “Selkie” ale.

The AquaFort Structure
With the UNH AquaFort, all three species are raised on a single platform system. The platform has two separate bays, which each hold a net. The fish school inside the net, and mussel lines and kelp lines hang around the outside, creating a biological “curtain” to ensure they maximize their impact on the fish waste. The platform itself is a floating frame made with HDPE, and it is anchored on two sides to prevent it from moving in the changing tides and current. The fish need to be fed and monitored daily, with their welfare and growth being priorities. The mussels and kelp thrive without much interference, and offer habitat for wild species like lumpfish and gunnel fish.


Where IMTA stands now
Trialing multiple seasons of IMTA with steelhead trout, kelp, and mussels has yielded exciting results. Not only does this strategy remove excess nutrients from the fish, but the kelp and mussels have sequestered additional nitrogen from the environment. This indicates that utilizing IMTA in regions that nitrogen and other nutrients are a concern might benefit the quality of the water, and ultimately help the environment.

The research on integrated multi-trophic aquaculture continues. Future aspects will look at land based IMTA, varying the species grown in AquaFort, and looking at expanding the AquaFort model to other parts of the United States, and beyond. Please check back to see additional publications and updates on the future of IMTA.

A pilot project to develop a bottom cage blue mussel aquaculture industry with offshore implantations.
Center leadership including David Fredriksson, Michael Chambers and researchers are working with NOAA partners Matthew Bowden, Richards Sunny and Lisa Milke to expand aquaculture opportunities in the Northeast by exploring bottom culture of shellfish using methods that do not require vertical lines, which reduces risk of entanglement by marine mammals, especially the critically endangered North Atlantic Right Whale.
This project, funded by the Atlantic States Marine Fisheries Commission, is exploring gear that can grow shellfish on the ocean bottom, but do not have rope going to the surface. Instead, retrieval rope is kept coiled on the bottom with a secured, small float. To monitor or harvest the shellfish, a device is activated to release a small float, uncoiling the rope to the surface so that the farmer can recover the gear. Three systems are being tested in NH waters. Two of which are remotely activated acoustic releases and the third a time released trigger.

The systems that utilize the acoustic releases are incorporated into wire mesh cages, like a lobster trap, so they can be deployed using fishing boat gear. To recover the bottom-mounted gear, a specific code is entered into a deck box unit that sends a unique signal to the release mechanism on the bottom. For one of the systems, the signal activates a mechanism unscrewing a component to release the rope and buoy to the surface. For the other system, the acoustic signal activates the release of compressed air from a tank filling a lift bag that brings the entire wire mesh pot to the surface, while still connected to the bottom shellfish gear with a rope. Once on the surface the rope is used to haul the shellfish cages.
The third system being investigated consists of a simple timed-released mechanism. The mechanism is set prior to deployment to releases a rope and buoy after a set amount of time. In this case the farmer can easily schedule a time to pick up the gear, while maintaining a farm without vertical lines.
Each of these methods is being tested at three sites off the coast of NH with the help of local shellfish farmers: Isles of Shoals Mariculture and Swell Oyster Company. We will also be collecting data on shellfish growth at each site. A bottom-mounted instrument package was also deployed at one of the sites to measure velocity profile (including at the level of the cages) along with temperature, dissolved oxygen, turbidity and chlorophyll-a. At the end of this study we will have a better understanding of some of the best methods shellfish farmers can use to raise blue mussels, scallops, and oysters while eliminating the need to keep vertical ropes in the water. This will ultimately contribute to a healthy and sustainable seafood community.
Video: A 30-second embedded video of Erich launching some gear off of Pete’s boat.

In a project led by Beth Zotter at Umaro Foods, members of the Center for Sustainable Seafood Systems, Michael Chambers, Zach Moscicki, Rob Swift and Igor Tsukrov are working in collaboration with Otherlab, Kelson Marine and Stationkeep LLC to develop an entanglement resistant, low-cost system for cultivating macroalgae, such as Saccharina latissima (sugar kelp) in the open ocean. The project is part of a larger national effort funded by the US Department of Energy ARPA-E’s MARINER program to develop technologies that can enable large-scale macroalgae cultivation for the purpose of generating material for sustainable food, feed and biofuel.
The novel farming system, as shown in Figure 1, is designed with limited use of rope that can pose an entanglement risk to marine animals, particularly when slack. Instead, the mooring and kelp substrate components are comprised of tensioned semi-rigid fiberglass rods that resist bending. We hypothesize that this would allow better shedding of the gear during a potential interaction event with marine mammals, however quantifying what would occur in such an event requires further study. The fiberglass rods used also break at a specific bending radius, so wrapping or knotting around flukes, flippers, jaws, etc. would be greatly minimized. The system is also feature minimal anchor scope (ratio of line length to depth) and helical embedment anchors; helping to minimize scenarios of reduced system tension.

In addition to addressing entanglement risks, the design must also be cost-effective. Therefore, to approach economic feasibility our system integrates: (1) minimized scope to reduce required seabed footprint, (2) using single novel multi-shaft helical anchors to support multiple mooring attachments, (3) an overlapping modular design to maximize horizontal growing area per farm area and provide flexibility for piecemeal farm expansion, (4) minimized mooring equipment scales and infrastructure through distribution of hydrodynamic loads to localized mooring points and (5) 0ptional wave-powered upwellers can be included to enhance nutrient availability to maximize growth rates.
The kelp farm was field tested at an Experimental Lease, granted to the University of New England by the State of Maine in Saco Bay. The system is shown in Figure 1 that combines an actual surface picture with a rendering of the submerged gear. It was deployed, seeded, and monitored at the site from November 2021 – May 2022. Though nearshore, the site is exposed to the open ocean and sees annual maximum wave heights on the order of 6.1 m (20 ft). Over 1800ft of kelp cultivation rod were planted over 4 farm modules.
Low cost and readily available, fiberglass rebar was tested as anchor and kelp cultivation components. A novel multi-shaft anchor was deployed using a robotic anchoring tool and tested as part of the farm mooring system. Helical anchors moored the low scope anchor lines and were tested for pull out strength at the end of the season. Tension loads on six anchor lines, waves and currents were also measured throughout the season. A prototype wave-powered upweller device was tested at a separate site. Together, the observations and data collected through this field season are helping to establish and test farm operations, validate our numerical modelling tools, inform our economic analysis, and evaluate the cultivation structure and component technology performance. Equipped with this data and tools we intend to iteratively improve our designs towards economic feasibility.
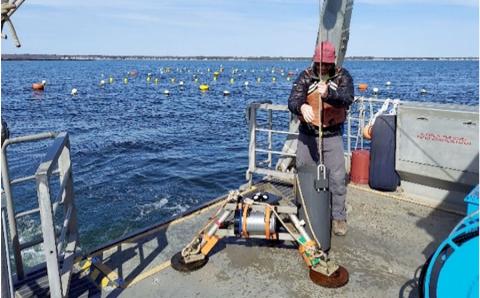



One area of focus for the Center is to conduct research to develop marine mammal-safe mooring Systems. In a project funded by the World Wildlife Fund (WWF) called “Advancement of Composite Kelp Cultivation Lines to Mitigate the Risk of Marine Mammal Entanglement” we are assessing the engineering properties of the fiberglass rebar that was deployed as a part of the project “Development and Testing of a Novel Macroalgae Cultivation System for Exposed and Offshore Environments.” This effort includes Graduate Students Louis Gitelman and Zachary Moscicki, UNH professors and research personnel Igor Tsukrov, Michael Chambers, Rob Swift, Noah MacAdam, and Sustainable Seafood Systems Director David Fredriksson. We are also working with industry partners Pete Lynn and Beth Zotter.
The significance of this research is immense. Entanglement in rope-based fishing gear has led to 27 of the 54 known deaths and serious injury events in the critically endangered North Atlantic Right Whale (NARW) from 2017 to 2022. While the fiberglass rebar shows great potential as an alternative to rope, engineering properties of the material used in this application are being investigated with the WWF funding. Laboratory tests are being conducted to examine tensile load capacities with terminations and breaking characteristics at specific forcing configurations related to NARW morphology.
As part of the project, a novel testing rig was developed as shown in the photo above right. Tests were conducted pulling on a sample of the fiberglass rebar at specific bending radius values. An inline load cell was used to measure force time series during the breaking process. This information is being used to assess potential whale loading configurations and how the fiberglass rebar responds.
Video: An example of a pull test using the rig to the point of breakage in bending.

Composite rod samples are also undergoing exposure experiments to determine their susceptibility to ocean water-induced degradation. The figure to the right shows biofouling growth that could affect material properties.
Figure left: Various varieties of composite rods undergoing long-term ocean water exposure testing.
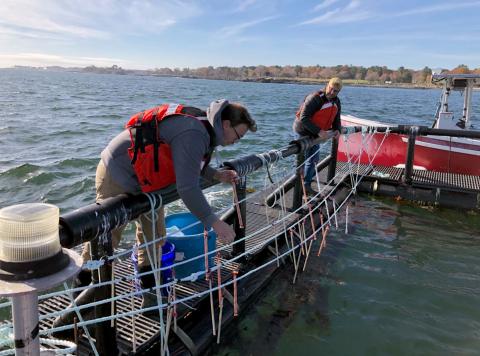
Traditional kelp farming requires hatcheries, which are time and labor intensive (Coleman et al., 2022a), and ropes for kelp substrate, which can be a potential hazard to whales and other marine life. At UNH, Mike Coogan and the Center for Sustainable Seafood Systems have partnered with Woods Hole Oceanographic Institution researchers Scott Lindell and Dave Bailey to optimize kelp seeding methodology and in an effort to address these two issues.
A pilot project is currently being conducted off the Integrated Multi-Trophic Aquaculture (IMTA) platform “Aquafort” in Portsmouth Harbor, NH. As part of the project, sugar kelp sporophytes were painted onto foot long pieces of fiberglass rebar using four different adhesion techniques each tested at four different drying times. Fiberglass rebar is a material being tested at UNH researchers as a whale safe alternative to the rope traditionally used in aquaculture and fishing.
The first adhesion technique involves simply painting the kelp sporophytes directly on the fiberglass rebar. The second treatment adds a binder to the fiberglass rebar after painting the sporophytes to potentially increase settlement. With the third technique the fiberglass rebar was wrapped with cotton gauze and the sporophytes were painted directly on the gauze without a binder. The last technique involves wrapping the fiberglass rebar with polyester braided rope and painting the sporophytes directly on the wrapping without a binder to better simulate traditional growing substrate.
After painting on the sporophytes using each technique, the footlong rods were allowed to dry for four different time intervals (0-10 min, 30 min, 60 min, 24 hours) before being suspended off the AquaFort for growout. The kelp will be left in the water for 2 months and growth and settlement will be monitored. By determining optimal drying times, we can potentially reduce the amount of time and resources the kelp uses on land and convert that into growth and environmental benefits in the water.



Center Director Dave Fredriksson is working with an interdisciplinary team from the University of Maine (Damian Brady, Struan Coleman, Adam St. Gelais, Kelly Cole), Kelson Marine (Toby Dewhurst, Michael MacNicoll) and Conscience Bay Research (Eric Laufer) in an effort to quantify the feasibility of using kelp as a method for Carbon Dioxide Removal (CDR).
While much more work is needed, especially to understand the ecological impact of this technique, the work has been published in Coleman et al., (2022a) and Coleman et al., (2022b).

Learn about how our Aquaculture researcher colleagues at the UNH College of Life Sciences & Agriculture (COLSA) are investigating new and innovative methods of sustainable fishing, reducing prevalence of aquatic animal disease, and leveraging the many ecosystem services that marine life can provide: